It’s easy to get caught up in the thrill of designing an eye-catching and informative label for a new product. You’ve probably spent hours considering the color scheme, images, and font size you’ll use, and have carefully deliberated over the best label material and finish for your product. But have you given any thought to the practicalities of label application?
This often-overlooked aspect of the label printing process can cause unnecessary setbacks and frustrations in the manufacturing of your product packaging if it is not carefully thought out. The key to efficient label application is determining the correct label unwind when designing your product’s labels.
In this article, we take a deep dive into everything you need to know about label unwind to ensure your label application goes as smoothly as possible.
What is label unwind?
Label unwind, or ‘roll direction’, simply refers to the orientation in which a label comes off the roll. In other words, label unwind describes the side of the label that peels off the roll first as a roll of labels is applied to product containers through a label applicator machine. For example, a roll of labels may be unwound right to left, in which case the right side will peel off first, or bottom to top, in which case the label will be applied onto the product from the bottom upwards.
Wound out and wound in labels
There are eight possible label unwind directions:
Four directions for labels printed on the outside of the roll material – ‘wound out’ labels
Four directions for labels printed on the inside of the roll material – ‘wound in’ labels
To conceptualize the difference between wound out and wound in labels, think of the two different ways in which you can place toilet paper on a dispenser: either, the roll can spin down towards you as you pull the paper (wound out labels), or the roll can spin back away from you as you pull the paper (wound in labels).
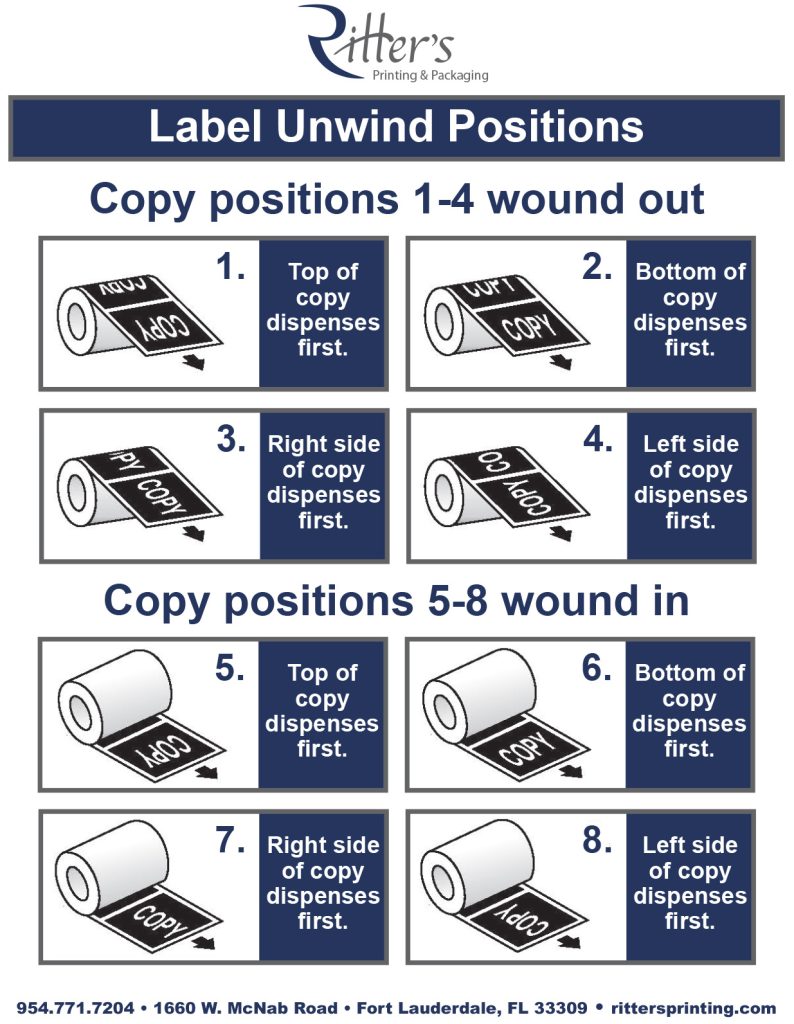
Most common roll directions
For both wound out labels and wound in labels, the roll direction can either be top first, bottom first, left first, or right first. For convenience, the label printing industry uses a standardized naming convention to refer to different label unwind directions.
Roll directions are given their names after the leading edge of the label that will peel off the roll first: a ‘left’ label unwind refers to an unwind where the left side peels off first, and a ‘right’ label unwind refers to an unwind where the right side peels off first, etc.
The standardized naming convention simply assigns a number to each roll direction: 1 to 4 are top, bottom, right, and left first for wound out labels; and 5 to 8 are top, bottom, right, and left first for wound in labels.
Why is understanding label unwind so important?
It is crucial to get your roll direction correct. If you don’t, your label will be applied upside down, or vertically instead of horizontally. If you are using a label applicator machine, you can’t afford to place an order with an incorrect label unwind – your entire roll of labels will be wasted and you’ll face a highly frustrating setback in getting your new product to market. In contrast, if you apply your labels manually, you may find that a particular roll direction is more suitable for faster application of labels by hand.
Label unwind direction can also have significant cost implications. When you are applying your labels manually, the label unwind direction you choose will directly impact the amount of waste the process produces and its overall efficiency. For example, depending on the size and shape of your labels, one roll direction may be more efficient and cost effective than another because of the impact it will have on the number of labels which can be printed across the ‘web’ (the continuous substrate of paper or film which the labels are printed on). As such, if you apply your labels manually, you may find that you choose your unwind direction based on cost considerations as opposed to other factors.
Determining roll direction for your labels
While understanding how label unwind works can be challenging, determining the correct label unwind to use should be straightforward, as your label applicator’s manual will indicate which roll direction the machine requires. If a manufacturer is applying your labels for you, you can contact them to find out which label unwind to order to ensure compatibility with their machines. You must confirm you have ordered labels with the correct roll direction: receiving a shipment of products with upside-down labels is the last thing you want for your business.
Label unwind considerations at the design stage
An important point to bear in mind, particularly at the label design stage, is that the roll direction, copy direction and dimensions of your label are all related. This is because we determine the left, right, top, and bottom sides of a label twith reference to the label’s copy, which always reads left to right and top to bottom (‘copy’ is the text that appears on your label).
In the case of top first and bottom first label unwinds, the copy will always print across the roll (that is, the text will read in a direction perpendicular to the roll direction). In the case of left first and right first label unwinds the copy will print with the roll direction (that is, the text will read in a direction parallel to the roll direction).
Note that in the label printing industry, when roll dimensions are given, the first measurement listed is always the leading edge of the roll, with the second measurement being the ‘repeat’ of the labels around the roll. A 3”x6” roll dimension will indicate a wide (or horizontal) label for left- or right first roll directions. By contrast, a 3”x6” roll dimension will indicate a tall (or vertical) label for top- or bottom first roll directions. For this reason, you will need to decide whether you want to produce a wide or tall label before you choose your roll direction and roll dimensions, to make sure that they are all compatible with one another.
Working with a label printing partner you can trust
If you feel unsure of the label application process, don’t panic. Your local label printing partner will be able to work with you to choose the appropriate label unwind for your product’s label. They will also be able to advise you on the roll directions which will work best with your label design, depending on the dimensions and copy direction of your label.
At Ritter’s Printing & Packaging, we enjoy working with our clients to help them create striking custom labels for products of all shapes and sizes. Our extensive range of label materials, finishes, and embellishments means that you will have the freedom to create the perfect label to suit your product and brand aesthetic.
With a reputation for delivering on-time and on-budget, there’s a reason why Ritter’s Printing & Packaging is the label printing partner of choice for so many businesses in the South Florida Tri-county area. To inquire about our label printing services contact us at 954-771-7204 today and we’ll gladly assist you!